Supplier Plant Visit at the World’s Largest Volvo Truck Manufacturing Facility, Part 2
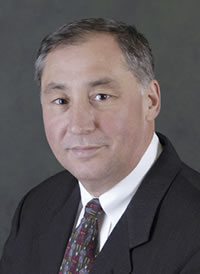
Robert Menard,
Certified Purchasing Professional,
Certified Professional Purchasing Consultant, Certified Green Purchasing Professional, Certified Professional Purchasing Manager
Editor’s note: This is the second part of a three part story about my visit to the Volvo plant in Virginia. It deals with many of the processes that make this plant a world class manufacturing facility. Click here for Part 1.
Kaizen, Kanbans, and “Kommunication”
Pardon the forced consonance in this sub-heading. Kaizen and kanban are well known Japanese words in manufacturing and “kommunication” looks more German than Japanese, but I digress. Volvo’s integration of technology, proven supply chain techniques, and human interaction combine to create a highly tuned operation.
A kanban refers to the logistics practice to enhance the flow of materials needed for production. It is not so much of an inventory control measure as it is a production control practice. The Japanese word refers to bill boards but evolved to the use of flags to indicate the need for parts replenishment.
Two bins of identical parts are co-located, sized to accommodate usage rate, product shape, and mass. In earlier iterations, when one bin was depleted, it was pulled off line, automatically triggering a brightly colored flag that would alert the stores replenishment technician to refill the bin. The second replacement bin usually slid forward under gravity. As technology advanced, and bins were bar coded, an automatic reader now knows by weight or movement that a bin is depleted and calls for replenishment. It also checks inventory levels against the Manufacturing Resource Planning (MRP) program to know if an order to a supplier must be placed.
Kaizen has evolved from concepts stemming back to post WW II economic reconstruction in Japan. It has come to be known as a process of “continuous improvement”. As such, it should be discussed at least on a daily basis. The Volvo shop and production floor is dotted with small (4-10 seats) glass paneled meeting rooms that host improvement suggestion meetings. These work stations and mini conference rooms epitomize the concept of kaizen.
As to external communication, the prospect of outsiders speaking directly with workers is discouraged, even verboten in many plants around the world. I always advise that such prohibitions are deal breakers for me and that if an attempt has been made to prepare the “interviewees” I will recognize it and make judgments accordingly.
I have demanded to visit the woman’s rest room in Latin American, Eastern European, Asian, and particular Middle Eastern countries. My interests are not political as much as personal. If women employees are treated poorly, how will the customer be treated, especially if the face of that customer is female?
Speaking to visitors at the Volvo plant was not prohibited; on the contrary, it was encouraged. Within bounds of life safety, any visitor can speak to any line or management employee.
What you can learn for the guy who does the work
I approached one fellow who was enjoying a snack break and we spoke of the transmissions he was installing. I still drive a manual shift car but I have heard much about continuously variable speed automatic transmissions (CVT)for heavy vehicles so I thought I’d ask him. I learned more than I knew and realized how much Volvo must invest in educating and training its employees.
He first said that the greatest impact was driver and public safety. Since the transmission automatically and continuously adjusts to load conditions, the driver’s attention is not distracted by shifting gears and the double clutching required by heavy duty manual transmissions. He added that the transmission was about the same size and weight of the conventional manual transmission but it provided better torque, efficiency, and durability. What is more, a CVT costs about the same or less and it created greater fuel efficiency and less noise.
That was another WOW revelation for me, a long recovering math/physics/engineering geek. Supplier plant visits truly are a learning experience.